40 Ton Explosion-Proof Bridge Crane Weld Inspection Report
Ultrasonic testing confirms flawless welds on critical crane components, ensuring safety& compliance with industry standards. High quality explosion proof crane for sale!
Purpose of the Inspection
The main goal of this inspection is to check the quality of the welds on the 40 Ton Explosion-Proof Bridge Crane. Welds are critical parts that hold the crane’s structure together. If they are weak or flawed, it can lead to safety risks or failures during operation. This inspection uses ultrasonic testing to find any hidden defects inside the welds that cannot be seen by the naked eye.
Importance of Ultrasonic Weld Inspection for Explosion-Proof Cranes
Explosion-proof cranes work in environments where safety is a top priority. Any spark or failure can cause serious accidents. Because of this, the welds must be strong and flawless to ensure the crane operates safely and reliably.
Ultrasonic testing is a reliable, non-destructive method to detect cracks, porosity, or other internal flaws in welds. It sends high-frequency sound waves into the weld and listens for signals that indicate defects. This helps prevent problems before the crane goes into use.
Regular weld inspections keep the crane safe and extend its service life. They also ensure compliance with industry standards and customer requirements.
Overview of the Crane Model and Scope of the Inspection
This inspection was done on the QB40T-22M model, a 40 Ton double girder overhead bridge crane designed for explosion-proof applications. The main focus was on the critical welds of the main girder, including:
- Top cover plates
- Bottom cover plates
- Web plates (vertical parts connecting top and bottom plates)
All butt weld seams in these areas were tested. The total weld length inspected was about 550mm to 1300mm per seam. The inspection covered 100% of the welds on these components to make sure no defects were missed.
The inspection was performed after the crane passed the initial visual check to confirm there were no obvious surface issues.
Product Information
QB explosion proof overhead crane for sale
The product inspected is a 40 Ton Explosion-Proof Bridge Crane, model QB40T-22M. This crane is specially designed to work safely in hazardous environments where explosion risks exist.
Product Identification Number
The specific unit inspected carries the identification number 220800936. This number helps track the inspection and ensures the report matches the exact crane.
Components Inspected
The ultrasonic weld inspection focused on key structural parts of the crane, including:
- Top cover plates — the upper horizontal plates of the main girder
- Bottom cover plates — the lower horizontal plates of the main girder
- Web plates — the vertical plates connecting the top and bottom cover plates
These parts are critical for the strength and stability of the crane’s main beam.
Material Specifications
The main materials used in these components are made from Q235B steel, a common structural steel known for good strength and weldability. This material choice supports both durability and safety requirements.
Thickness of Materials Inspected
The thickness of the parts tested during inspection is as follows:
- Top cover plate: 14 mm
- Bottom cover plate: 14 mm
- Web plate: 6 mm
These thicknesses are typical for a 40-ton crane, ensuring the crane can handle heavy loads safely.
Inspection Methodology
Weld Type
- Butt welds with flat welding, joining steel plates edge to edge.
Inspection Technique
- Ultrasonic Testing (UT) used to detect internal weld defects without damaging the material.
- High-frequency sound waves reflect off any flaws inside the weld.
Equipment Used
- Ultrasonic flaw detector: CTS-22B
- Probe model: 2.5P13×13K3, suitable for the material thickness.
Scanning Approach
- Zigzag double-sided scanning for thorough coverage of both sides of weld seams.
Surface Preparation and Couplant
- Weld surfaces shot blasted to remove contaminants and improve signal quality.
- Chemical paste couplant applied to aid sound wave transmission.
Standards and Criteria
Inspection followed JB/T10559-2006 national standard.
Welds evaluated by grade:
- Top cover plate: Grade III
- Web plate: Grade II
- Bottom cover plate: Grade I
Timing of Inspection
- Conducted after passing visual inspection to avoid interference from surface defects.
Sensitivity Settings
- Equipment set at DAC—36 dB to ensure reliable detection of critical flaws.
Coverage
- 100% of weld seams inspected to guarantee no defects were missed.
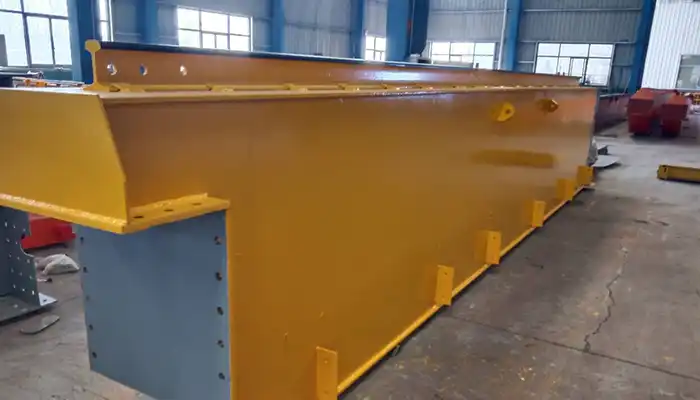
main girder of 40 ton explosion proof overhead crane for sale Germany
Inspection Procedure
Step-by-Step Outline
The inspection followed a detailed and careful process to ensure every weld was checked thoroughly. The steps included cleaning, calibration, scanning, and evaluation to catch any defects inside the welds.
- The weld surfaces were first cleaned by shot blasting to remove rust, dirt, and any coatings.
- The ultrasonic flaw detector was calibrated using a standard reference block to guarantee accurate readings.
- Chemical paste couplant was applied on the weld surface to help transmit ultrasonic waves effectively.
- The inspector scanned the welds using the CTS-22B ultrasonic tester with a 2.5P13×13K3 probe.
- Scanning was performed in a zigzag pattern on both sides of each weld seam for complete coverage.
- The operator monitored the device screen carefully for any signals that indicated defects.
- All inspection data were digitally recorded for later analysis and reporting.
- Welds were then evaluated against acceptance criteria according to the JB/T10559-2006 standard.
Areas and Weld Lengths Inspected
The inspection focused on the main load-bearing parts of the crane’s main girder. These areas include the critical welds that connect the plates forming the beam structure.
- Butt welds on the top cover plates were inspected.
- Butt welds on the bottom cover plates were inspected.
- Butt welds on the web plates (vertical connecting plates) were also tested.
- The length of each weld inspected ranged between 550 mm and 1300 mm, depending on the specific part.
Data Recording and Analysis
The collected data was carefully saved and analyzed to ensure no flaws were missed. Each signal was reviewed against set standards to determine the weld’s integrity.
- Ultrasonic readings were saved electronically for traceability.
- The inspector reviewed all signals to identify any abnormal reflections indicating defects.
- Suspected defects triggered a rescanning process to confirm findings.
- The results were compared against the acceptance levels defined in the inspection standard.
Quality Control Measures
Strict quality control steps were followed throughout the inspection to maintain high accuracy and reliability. These measures ensured the inspection results are trustworthy and meet industry requirements.
- Equipment was calibrated before the inspection started to ensure accuracy.
- Only trained and certified inspectors carried out the ultrasonic testing.
- A visual inspection was performed first to catch any obvious surface problems.
- The entire weld length was covered, with no sections skipped.
- A second technician verified all inspection records and data to confirm reliability.
Inspection Results
Summary of Findings for Each Weld Area
The ultrasonic inspection covered all critical weld areas on the crane’s main girder. Each area was thoroughly checked for internal flaws to ensure structural integrity.
- Top cover plate welds: No internal defects were detected throughout the inspected length.
- Bottom cover plate welds: The inspection showed clean welds without any flaws.
- Web plate welds: All weld seams were free from any ultrasonic indications of defects.
Evaluation Grades Applied
The welds were evaluated according to the standards and assigned different grades based on their location and criticality. These grades reflect the acceptance criteria used for each weld area.
- Top cover plate welds were evaluated as Grade III.
- Web plate welds were evaluated as Grade II.
- Bottom cover plate welds were evaluated as Grade I.
Detected Defects or Lack Thereof
No weld defects exceeding the acceptance criteria were found during the ultrasonic inspection. This means all welds met the required quality standards for safety and performance.
- No cracks, porosity, or lack of fusion were detected.
- No unacceptable indications of internal flaws were present.
- The welds passed the inspection fully, showing excellent workmanship.
Visual Inspection Verification
Before the ultrasonic inspection, a visual check was done to confirm the surface condition of the welds. This ensured no obvious surface defects could interfere with the ultrasonic results.
- All welds passed the visual inspection with no surface cracks, undercuts, or other visible flaws.
- Visual confirmation supported the ultrasonic findings, reinforcing the overall weld quality.
Conclusion
Overall Assessment of Weld Quality
The ultrasonic inspection confirmed that the weld quality on the 40 Ton Explosion-Proof Bridge Crane is excellent. All critical welds showed no signs of internal defects, ensuring the crane’s structural integrity and safety.
Confirmation of Compliance
The inspection fully complied with the JB/T10559-2006 standard. All testing procedures, sensitivity settings, and evaluation criteria were met according to this regulation, guaranteeing industry-standard quality control.
Statement on Weld Quality
- All inspected welds meet the required quality standards.
- No unacceptable defects were found in any weld seam.
- The crane’s main girder welds are safe and reliable for operation in explosion-proof environments.
Date of Inspection and Certification Validity
- The ultrasonic weld inspection was conducted in February 2023.
- The certification issued from this inspection remains valid as long as no structural changes or damages occur to the welds.