Case Study: 1 Ton KBK Crane, 54-Meter Runway for Sale Philippine
A lightweight 1-ton KBK crane efficiently covers a 54-meter runway, improving material handling in a compact Philippine workshop.
Project Background
Client Overview
The client is a local service company based in the Philippines. They handle light equipment assembly and routine maintenance for their own industrial customers. Their workshop is long and narrow, which makes material movement challenging.
They often move small but heavy parts—mostly under 1 ton. Before this project, their team used manual carts and mobile lifting tools. It was time-consuming and tiring, especially over long distances.
They wanted a safer and more efficient way to move materials across the full length of their workshop—around 54 meters long.
Project Objectives
The client had two clear goals in mind:
- Make material handling easier and faster
They needed to cut down the time workers spent walking or wheeling heavy parts along the workshop. Lifting should be simple and controlled. - Install a lightweight system without major changes to the building
Their workshop had limited ceiling height and couldn't support a heavy overhead crane. A compact, light, and modular crane system was the right fit.
They also wanted something reliable and easy to maintain. Power supply was fixed at 400V, 60Hz, 3-phase, so the system had to match that.
In short, the customer was looking for a practical, safe, and space-saving crane solution.
kbk crane for sale for your reference
Challenges Faced by the Client
Limited Ceiling Height
One of the first things we noticed during the design stage was the low ceiling height in the client's workshop. The available headroom was tight, leaving little vertical space for a standard hoisting system.
- The client needed to lift parts and components weighing up to 1 ton to a height of around 9.5 meters.
- However, a traditional wire rope hoist or large overhead crane would have eaten up too much space.
- There were also obstructions in the ceiling—lighting fixtures, air ducts, and existing support beams—which made layout planning more complicated.
We recommended using a compact electric chain hoist combined with a low headroom trolley. This reduced the total height of the lifting unit and allowed the client to maximize usable lifting height. It was also easier to install around existing roof structures without cutting or relocating them.
Lightweight Crane System for a 54-Meter-Long Workshop
The workshop was long—about 54 meters in working length. The client needed a crane that could move materials from one end of the building to the other smoothly and without delays.
- A standard overhead crane made of heavy steel beams would have been too much for the building’s current structure to support.
- Reinforcing the entire ceiling or installing large columns was not ideal—it would be expensive and take a lot of time.
- They also wanted to avoid using up floor space with added supports.
This made a KBK modular rail system the most suitable option. It’s made of high-strength cold-rolled steel, which is strong but lightweight. It can span long distances without needing large support structures.
We divided the 54-meter runway into sections for shipping and on-site assembly. This not only made transportation easier but also allowed flexible layout adjustments during installation.
Quick Installation with Minimal Disruption
The client couldn’t afford to pause their operations for long. The workshop had ongoing projects and regular deliveries.
- A typical overhead crane installation could take several weeks, especially if it requires custom structural work or heavy equipment.
- The client needed a faster solution with limited downtime.
- They also wanted the installation process to be safe and clean, without disrupting the workflow of their employees.
With this in mind, we designed the crane system for bolt-together assembly. Most parts were pre-fabricated at our factory and shipped in labeled sections. On-site work focused on anchor placement, support frame setup, and final alignment.
We completed the full installation in stages—starting from one end and working forward—so part of the workshop could remain in use during the process.
Power Compatibility: 400V / 60Hz / 3-Phase
Power supply issues can cause serious problems if not considered early. In this case, the client operated on a 400V, 60Hz, 3-phase power supply, which is standard in many parts of the Philippines.
- Some crane systems—especially those designed for the Chinese or European market—are built for 380V / 50Hz.
- Using a crane with mismatched voltage or frequency could cause motor failures, poor performance, or even safety risks.
We selected an electric chain hoist and control panel that matched the local voltage and frequency exactly. This avoided the need for external transformers, reduced setup time, and ensured stable long-term operation.
It also meant easier access to replacement parts and support if needed in the future.
In summary, the client faced several realistic and practical challenges: limited headroom, a long handling distance, the need for fast setup, and specific power requirements. Our KBK system, combined with a compact chain hoist, was the right solution to meet all of these needs in a safe, simple, and cost-effective way. Check more on types of overhed cranes for sale the Philippines.
Proposed KBK Crane Solution
Crane Type: 1 Ton KBK Modular Overhead Crane
To meet the client’s specific handling needs, we proposed a 1-ton KBK modular overhead crane system. This system was the best match for their long, low-ceiling workshop and their need for flexible material handling.
The KBK system uses lightweight, cold-formed steel rails and a suspension structure. It’s designed for light-duty applications and is very adaptable to different workshop layouts. That flexibility was key for this project.
Key Specifications
We tailored the crane’s specifications to the exact requirements of the client’s facility and operation. Below are the major specs of the solution we provided:
- Lifting capacity:
The crane can safely lift loads up to 1 ton, which is more than enough for the components the client regularly handles. - Lifting height:
The hoist can lift materials up to 9.5 meters, ensuring maximum use of vertical space despite the workshop’s low ceiling. - Crane span:
The effective span of the crane (across the width of the workshop) is 4 meters, allowing for smooth left-to-right movement along the work area. - Runway length:
The total runway length is 54 meters, allowing the crane to travel the full length of the workshop. This includes a custom steel support structure tailored to the workshop’s frame. - Power supply:
The crane operates on 400V, 60Hz, 3-phase, matching the local power standard in the Philippines. No voltage converters or special adapters were needed. - Electric chain hoist:
We equipped the crane with a durable electric chain hoist. It was chosen for its low headroom, precise load control, and easy maintenance.
Customization Highlights
Every KBK system we deliver is customized. For this project, several details were tailored to fit the client's workshop and usage.
Modular Track System Tailored to the Layout
- The KBK tracks were configured according to the layout and working flow of the workshop.
- We used standard modular components but adjusted the track spacing, span, and suspension positions to match real measurements on-site.
- This ensured the crane covered all the required workstations without wasting space.
Steel Structure Designed for Facility Fit
- Because the workshop couldn’t support a ceiling-mounted crane, we designed a freestanding steel frame to support the entire runway.
- The structure was calculated to carry both static and dynamic loads safely.
- Column spacing and beam height were customized to avoid any interference with floor equipment or roof obstacles.
Chain Hoist Selection Based on Actual Use
- The chain hoist was selected based on lifting height, frequency of use, and load type.
- We chose a compact, low-headroom model to maximize lifting height under the low ceiling.
- The hoist included features like dual-speed lifting, overload protection, and a push-button pendant control for ease of use.
In short, this KBK crane system was not just off-the-shelf—it was carefully engineered to meet the client's space limitations, workflow needs, and safety expectations. It offered a complete solution that was lightweight, modular, and efficient, while still being durable enough for everyday industrial use. kbk rails
steel structure of kbk crane, the columns
1 ton electric chain hoist and the pendant control
Implementation Process
Engineering & Design
This phase started with understanding the real conditions of the client’s workshop. It was more than just fitting a crane—it had to work smoothly with what was already in place.
Layout Planning Based on Actual Workshop Dimensions
- The client shared detailed workshop drawings and measurements, including height, width, column positions, and obstacle zones.
- We used this data to create a customized CAD layout for the KBK system.
- The crane’s span, hoist travel path, and runway beam alignment were carefully planned to avoid interfering with existing structures like lighting, ducts, or machinery.
- We ensured the 54-meter runway was divided into manageable sections for easier shipping and assembly.
Load Testing and Structural Compatibility Checks
- Before finalizing the design, we ran structural load calculations to confirm that the freestanding steel structure could support the crane and hoist system safely.
- The support columns, base plates, and anchor bolts were designed according to local building safety standards.
- Simulated load testing was conducted in-house to verify hoist performance and the behavior of the KBK rails under full load.
- All components passed CE and ISO safety standards, which added peace of mind for the client.
Manufacturing & Delivery
Once the design was approved, we moved quickly into production. We ensured that every component—from steel supports to hoists and rails—was manufactured to exact specs.
Production Timeline
- The main production took about 25 working days. This included fabrication, quality inspection, painting, and packaging.
- Hoist units, electrical panels, and track segments were tested individually before packing.
- The modular KBK tracks were cut into transportable lengths with labeled parts for easy reassembly.
Shipping to the Philippines
- The complete crane package was packed into steel-framed wooden crates for safe international shipping.
- All items were sent by sea freight, using a containerized shipment from our port in China to the client's delivery address in the Philippines.
- Shipping took approximately 18 days, depending on customs clearance.
- A detailed packing list and installation manual were included with the shipment.
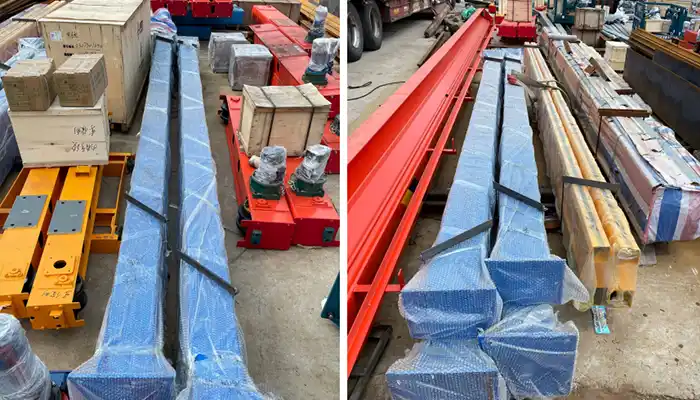
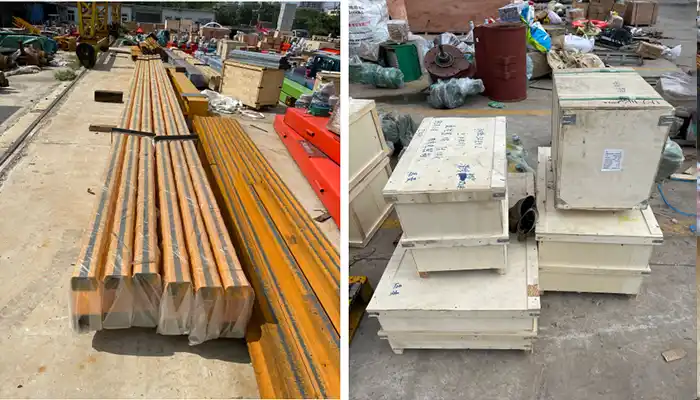
Installation Support
We knew the client needed fast setup with minimal interruption to their work. That’s why we provided flexible installation support options.
Remote Guidance & Documentation
- A complete set of installation drawings, step-by-step guides, and wiring diagrams was prepared in English.
- Our engineers stayed in contact with the client’s team by video calls and messaging to support each installation step.
- Remote troubleshooting was also available in case of any unexpected issues during setup.
Optional On-Site Support
- For clients needing direct help, we offered on-site installation service as an option (subject to travel and entry policies).
- In this case, the client had an experienced maintenance team, so remote support was enough.
- The KBK track system and runway beams were bolted and connected as planned.
- The electric hoist was hung and tested on-site, with load testing carried out before full commissioning.
This whole process—from planning to delivery to setup—was completed within about 8–10 weeks. The client was able to begin using the crane immediately after installation, without having to modify their building or interrupt production for long. That’s one of the biggest advantages of a modular KBK overhead system—it’s easy to engineer, quick to install, and simple to maintain.
Results & Performance
Operational Benefits
After the installation of the 1-ton KBK modular overhead crane, the client experienced noticeable improvements in their material handling process. The crane system solved several pain points and brought real value to their day-to-day operations.
Seamless Material Movement Across the 54-Meter Runway
- The KBK crane now allows smooth and continuous movement of materials along the entire 54-meter workshop length.
- Previously, materials were moved manually or with push carts, which took more time and effort.
- Now, a single operator can control the movement of materials from one end of the facility to the other without delays.
- The long runway has created a more efficient material flow, improving overall productivity.
Improved Operator Efficiency and Workplace Safety
- The crane’s pendant control system makes operation simple and safe.
- The electric chain hoist comes with dual-speed lifting, which helps operators handle both quick transfers and precise positioning.
- Because the crane is suspended from above, there’s no interference with ground activities.
- This setup keeps the work floor safer and reduces the chance of accidents or load mishandling.
- It also reduces the need for manual lifting, which helps lower physical strain on workers.
Reduced Floor Congestion and Better Space Utilization
- By moving material handling off the ground, the client freed up valuable floor space.
- The cleaner layout has improved traffic flow for both people and equipment.
- The workshop now has more flexibility for future layout changes or equipment additions.
- With fewer obstructions on the floor, maintenance and housekeeping tasks have also become easier.
Customer Feedback
The client provided positive feedback across different stages of the project—from installation to regular daily use.
Smooth Installation Process
- The KBK crane system was delivered with detailed drawings and labeled parts, making it easy for the local team to install.
- Even though the system included a 54-meter runway and steel support structures, the client’s team completed the setup with remote guidance.
- Installation was done without major disruption to the workshop’s normal production schedule.
Simple Operation and Easy Maintenance
- Operators picked up the crane controls quickly with minimal training.
- The electric chain hoist runs smoothly and handles loads between 300 kg to 800 kg regularly.
- The low-headroom design matched the limited ceiling height and still provided the required lifting height of 9.5 meters.
- Routine maintenance is straightforward thanks to easy access to lubrication and inspection points.
Strong After-Sales Support
- The client appreciated the quick technical support during installation and early operation.
- All questions regarding wiring, settings, and adjustments were handled quickly through email or video call.
- The client felt confident that long-term support would continue to be available when needed.
Summary of Results
The 1-ton KBK crane system fully covered the 54-meter workshop span, allowing smooth and efficient material transfers. Operator productivity improved thanks to the easy-to-use overhead design, which also helped free up valuable floor space.
The electric chain hoist performed reliably during daily operations, even with limited headroom. The client was satisfied with both the crane’s performance and the support provided. Overall, the system met all project goals and proved to be a practical solution for lightweight, long-span lifting in a compact workshop.
KBK cranes work really well for long-distance, light-duty lifting tasks, especially in workshops where space or ceiling height is limited. Their lightweight and modular design means they don’t require heavy support structures, so they fit easily into existing buildings without big changes.
The modular runway system is another big advantage. It allows the crane track to be extended, shortened, or moved if needed. This makes it easy for businesses to expand or rearrange their workspace without much hassle or extra cost. Changes can be done quickly, reducing downtime and keeping operations running smoothly.
Finally, customizing the crane based on the client’s exact needs helps speed up delivery and installation. When a solution is tailored for factors like runway length, lifting height, and power supply, it fits perfectly and works right away. This is especially helpful for international clients, because it means the crane can be shipped and set up faster, with less disruption and a quicker return on investment.
Yuantai Crane is a certified Chinese manufacturer with CE and ISO certifications, ensuring high-quality standards. We have many years of experience exporting cranes to countries in Southeast Asia. Our specialty is in light-duty modular cranes and custom crane systems designed to meet the specific needs of different industries and workshops.