Choosing Right Overhead Crane & Gantry Crane for Your Flour Mill
Flour mill cranes for sale. Check all types of overhead cranes & gantry cranes for flour mills to select right floor mill material handling cranes to ensure safety.
Choosing the Right Overhead Crane for Your Flour Mill: Factors to Consider
In the bustling world of flour milling, where precision and efficiency are essential, the choice of an overhead crane becomes a strategic decision that can significantly impact the success of operations. Flour mills are dynamic environments, constantly handling a variety of materials, from raw grains to the fine, powdery product they are known for. It is within this intricate setting that the importance of selecting the right overhead crane becomes apparent.
Importance of Selecting the Right Overhead Crane
Selecting the right overhead crane is not merely a matter of preference; it's a fundamental requirement. Overhead cranes are workhorses of the industry, facilitating the movement of raw materials, finished products, and everything in between. Their role is so integral that the choice of crane type, tonnage, and safety features can influence not only the efficiency of operations but also the well-being of the workforce and the integrity of the product.
Dust free overhead crane with underhung crane design for flour mill
Flour Mill Operations and Diverse Material Handling Needs
Flour mills operate at the crossroads of agriculture and food production, where raw grains are transformed into a staple consumed by millions worldwide. This dynamic process involves various stages, from receiving and storing raw grains to the precise handling of milled flour and the maintenance of equipment and machinery.
Each of these stages demands specific material handling solutions. The delicate task of handling flour requires precision, while the transport and positioning of heavy equipment necessitate strength and versatility. Flour mills operate on a 24/7 schedule, making seamless material handling a vital element of their success.
Balancing Efficiency and Safety in Material Handling
Efficiency is the lifeblood of flour mills. The ability to process and deliver flour to market swiftly is essential for meeting the demands of a growing global population. However, in the quest for efficiency, safety cannot be compromised.
Balancing efficiency and safety is a constant challenge in flour milling. This is where the right overhead crane plays a pivotal role. It ensures materials are handled swiftly and precisely, reducing downtime, while also safeguarding personnel and the product itself.
In the following sections, we will delve into the critical factors that guide the selection of the right overhead crane for your flour mill. We will explore operational needs, crane types, tonnage considerations, the choice between explosion-proof and standard cranes, and the role of advanced technology in modernizing material handling. Furthermore, we will address the importance of compliance with safety and environmental regulations, the impact of environmental responsibility, and the lessons learned from past crane safety incidents. Finally, we will conclude by highlighting the enduring partnership between flour mills and overhead cranes, a relationship that continues to flourish in the ever-evolving world of flour milling.
Identifying Operational Needs
To select the right overhead crane for your flour mill, the first step is to identify and understand the specific operational needs. Flour milling involves a diverse range of tasks, each with its unique requirements when it comes to material handling. Two primary aspects that warrant consideration are raw material handling and equipment maintenance and positioning.
Raw Material Handling
Tonnage Requirements for Incoming Grains and Ingredients
Flour mills receive a constant influx of raw materials, primarily in the form of grains and various ingredients. The tonnage requirements for handling these materials can vary significantly. When selecting an overhead crane, it's crucial to determine the maximum weight and volume of materials being transported. This information helps in choosing a crane with the appropriate tonnage capacity to ensure smooth and efficient handling.
- Grains: Raw grains are the backbone of flour milling. Depending on the scale of your operations, these grains may arrive in vast quantities. Overhead cranes used for unloading grain shipments must have the capacity to handle these heavy loads safely.
- Ingredients: In addition to grains, flour mills use various ingredients in their processes. These ingredients come in different forms, such as bags or bulk containers. The crane used for ingredient handling should be capable of precise and safe positioning, especially in areas where hygiene is paramount.
Precision and Hygiene Considerations for Flour Handling
When it comes to handling the finished product—flour—precision and hygiene are of utmost importance. The crane responsible for flour handling should meet stringent hygiene standards to ensure product integrity. Contamination or spillage can lead to quality issues and potential health hazards.
- Hygiene Standards: Overhead cranes used for flour handling should be designed with features that promote hygiene. This includes sealed components, easy-to-clean surfaces, and materials that are suitable for food handling.
- Precision Control: The crane's control system should allow for precise load positioning, minimizing the risk of spillage or contamination. This is particularly important when transferring flour to packaging or storage areas.
Equipment Maintenance and Positioning
Requirements for Maintenance Tasks and Machinery Positioning
Flour mills are home to an array of equipment and machinery that require regular maintenance. This includes cleaning, repairs, and machinery positioning for maintenance purposes. When selecting an overhead crane for these tasks, it's essential to consider the types of equipment involved and their specific requirements.
- Versatility: The crane used for maintenance tasks should be versatile and adaptable to various equipment types. Equipment positioning may require precise load control and the ability to reach tight spaces within the mill.
- Localized Material Handling: In many cases, maintenance tasks are localized, meaning they don't involve large-scale material handling. Jib cranes, with their localized operation and articulating capabilities, are often ideal for these scenarios. They provide the necessary flexibility for maneuvering around equipment and machinery.
Versatility and Localized Material Handling
The versatility of overhead cranes is a key consideration when it comes to equipment maintenance and positioning. Flour mills may have a wide range of machinery, from mixers to conveyors, and each requires precise handling for maintenance and repairs.
- Jib Cranes: Jib cranes are particularly useful for localized material handling tasks in flour mills. Their articulating jib allows for easy access to equipment, while their versatility and ability to rotate provide flexibility in positioning loads accurately.
Identifying and understanding your flour mill's operational needs, whether they pertain to raw material handling or equipment maintenance, is the foundation for selecting the right overhead crane. This ensures that the crane chosen is not only capable of handling the required tonnage but also meets the precision, hygiene, and versatility standards that are essential in the world of flour milling.
Choosing the Appropriate Crane Type
Once the operational needs of your flour mill are identified, the next crucial step is to choose the appropriate crane type. Flour mills can benefit from a variety of crane designs, each tailored to specific tasks and operational demands. Let's explore the options available:
Bridge Cranes- Single vs. Double Girder Designs
Bridge cranes, also known as overhead traveling cranes, are a common sight in flour mills due to their adaptability and load-bearing capabilities. When considering bridge cranes, it's essential to decide between single and double girder designs:
- Single Girder Bridge Cranes: These are a cost-effective solution for handling lighter loads. Single girder cranes are versatile and can efficiently manage tasks like raw material handling and equipment maintenance.
- Double Girder Bridge Cranes: Double girder cranes are robust and suited for handling heavier loads. They offer increased stability and precision, making them an excellent choice for large-scale raw material handling and machinery positioning.
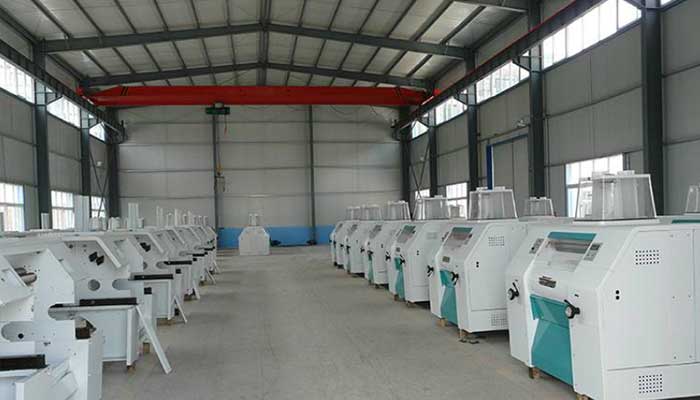
Gantry Cranes- Outdoor and Indoor Applications
Gantry cranes provide a versatile material handling solution in flour mills. They offer the advantage of being mobile, allowing them to cover a broader areGantry cranes can be classified into outdoor and indoor types:
- Outdoor Gantry Cranes: These cranes are engineered to withstand various weather conditions, making them suitable for outdoor material handling. They are often used in the storage and loading/unloading of raw materials.
- Indoor Gantry Cranes: Designed for indoor use, these cranes are ideal for tasks that require precision and localized material handling within the controlled environment of the mill.
Jib Cranes- Versatility and Localized Material Handling
Jib cranes are known for their versatility and localized material handling capabilities. In a flour mill, where maintenance tasks may require precise positioning, jib cranes are indispensable. Key considerations for jib cranes include:
Explosion-Proof Cranes
Safety Considerations for Potentially Explosive Dust Environments
Flour mills present a unique safety challenge due to the presence of potentially explosive flour dust. Explosion-proof cranes are specially designed to operate safely in such environments.
- Specialized Components and Enclosures: Explosion-proof cranes are equipped with specialized components and enclosures that prevent the risk of ignition in the presence of combustible dust. This includes explosion-proof motors, control panels, and enclosures.
- Safety Features: These cranes are designed to minimize the risk of sparks and electrical malfunctions, incorporating safety features such as anti-static measures and grounding.
Selecting the appropriate crane type is essential for optimizing your flour mill's material handling processes. Whether it's the adaptability of bridge cranes, the mobility of gantry cranes, the precision of jib cranes, or the safety of explosion-proof cranes, the right choice will enhance the efficiency and safety of your operations.
Explosion proof double girder overhead crane for flour mill
Explosion-Proof vs. Standard Cranes in Flour Mill
In the potentially explosive environment of a flour mill, the choice between explosion-proof and standard cranes is a critical decision. Safety, cost-effectiveness, and regulatory compliance are at the forefront of this choice, demanding careful consideration.
Safety Considerations
Balancing Safety and Cost-Effectiveness
Safety is a top priority in flour milling, especially when dealing with combustible flour dust. The choice between explosion-proof and standard cranes involves striking a balance between safety and cost-effectiveness. Key considerations include:
- The Risk of Combustible Dust: Flour mills are known for the presence of fine, airborne flour dust. In the event of an electrical or mechanical malfunction, this dust can ignite, potentially leading to explosions. Explosion-proof cranes are designed to minimize the risk of such incidents.
- Safety Features: Explosion-proof cranes come equipped with specialized safety features, such as explosion-proof motors, wiring, and control panels, which reduce the risk of sparking and ignition in the hazardous environment.
The Significance of Explosion-Proof Features in Flour Mills
Explosion-proof features are not mere luxuries but absolute necessities in the flour milling industry. They play a significant role in ensuring the safety of personnel and protecting the product from contamination. Understanding their significance is paramount:
- Personnel Safety: Explosion-proof cranes are essential for safeguarding the workforce in the event of an electrical fault. The explosion-proof design reduces the risk of catastrophic accidents, protecting employees from harm.
- Product Integrity: In a sector where hygiene is paramount, explosion-proof cranes prevent product contamination due to sparks or electrical malfunctions. This ensures that the integrity of the flour remains intact.
Cost-Benefit Analysis
Assessing Initial Costs vs. Long-Term Safety and Regulatory Compliance
While explosion-proof cranes may come with higher upfront costs compared to standard cranes, a comprehensive cost-benefit analysis reveals the long-term advantages of investing in safety. Considerations include:
- Long-Term Safety: Explosion-proof cranes are an investment in long-term safety. They minimize the risk of accidents and potential regulatory fines, contributing to a safer work environment.
- Regulatory Compliance: Choosing explosion-proof cranes ensures compliance with safety and environmental regulations specific to the flour milling industry. Non-compliance can lead to costly fines and legal consequences.
Regulatory Compliance
Meeting Safety and Environmental Regulations in Flour Milling
Flour mills operate within a regulatory framework that addresses both safety and environmental concerns. Compliance with these regulations is not just a legal obligation but a moral responsibility. Key considerations include:
- Safety Regulations: Flour mills must adhere to industry-specific safety regulations to protect their workforce and ensure safe crane operations in potentially explosive environments.
- Environmental Regulations: Environmental responsibility is a fundamental aspect of flour milling. Mills are often located in proximity to residential areas, making strict adherence to environmental regulations governing emissions, waste management, and noise control crucial.
The choice between explosion-proof and standard cranes is more than a financial decision; it is a commitment to safety and regulatory compliance. In the delicate ecosystem of a flour mill, the investment in explosion-proof cranes ensures not only the well-being of the workforce but also the continued success of the operation, free from the devastating consequences of dust-related accidents.
Sizing for Efficiency
Efficiency is the lifeblood of flour mills, and the sizing of overhead cranes plays a pivotal role in achieving this goal. Properly matching crane capacity to operational demands ensures seamless material handling and can prevent bottlenecks that hinder productivity. Additionally, precision load control is essential for maintaining load stability and preventing overloading.
Evaluating Tonnage Requirements
Matching Crane Capacity to Operational Demands
The heart of sizing for efficiency lies in evaluating tonnage requirements and ensuring that the selected crane has the capacity to handle the loads efficiently. Key considerations include:
- Raw Material Handling: The tonnage requirements for incoming grains, ingredients, and flour must be assessed. This information guides the selection of a crane with the appropriate lifting capacity, ensuring that materials can be handled swiftly and safely.
- Equipment Maintenance: Maintenance tasks often involve positioning heavy machinery and equipment components. A crane must have the capacity to manage these loads to facilitate maintenance efficiently.
Efficient Material Handling
Avoiding Bottlenecks and Optimizing Productivity
Efficient material handling is a cornerstone of flour mill operations. Crane sizing should be optimized to prevent bottlenecks in the material flow and ensure that the entire process operates smoothly. Key points to consider include:
- Load Balancing: Balancing the workload among multiple cranes can prevent overloading and congestion. This load balancing should be incorporated into the crane design and operational strategy.
- Optimizing Workflows: Cranes should be strategically positioned to optimize the flow of materials and minimize the time required for handling. This ensures that operations remain productive and that resources are used efficiently.
Precision Load Control
Preventing Overloading and Maintaining Load Stability
Precision load control is essential for preventing overloading and ensuring the stability of the load during material handling. Key factors include:
- Load Monitoring: Overhead cranes should be equipped with load monitoring systems that provide real-time data on the load's weight and stability. This information allows operators to make precise adjustments during handling.
- Safety Considerations: Overloading a crane can lead to accidents, equipment damage, and product loss. By maintaining load stability and preventing overloading, the risk of such incidents is significantly reduced.
Sizing cranes for efficiency is not only about matching tonnage requirements but also about optimizing the entire material handling process. It involves preventing bottlenecks, ensuring load stability, and using cranes strategically to maximize productivity. When cranes are appropriately sized and utilized, flour mills can achieve the efficiency and precision that are vital for success in this dynamic industry.
Modernizing with Technology
In the ever-evolving landscape of flour milling, modernizing material handling with technology is imperative for efficiency and safety. Overhead cranes can benefit from advanced technologies that enhance precision, reduce manual handling risks, and improve overall operations. Let's explore how technology can be harnessed for these purposes:
Incorporating Advanced Technology
Remote Control Capabilities for Safe Operations
In the digital age, remote control capabilities have revolutionized crane operations. This technology allows operators to control cranes from a safe distance, providing several advantages:
- Safety: Remote control minimizes the need for operators to be in close proximity to moving loads, reducing the risk of accidents and injuries.
- Precision: Operators can have a clear view of the entire operation, making it easier to position loads accurately and avoid obstacles.
Load Sensing for Precision
Load sensing technology provides real-time data on the weight and balance of the load being handled. This information is invaluable for maintaining precision during material handling:
- Preventing Overloading: Load sensing systems ensure that cranes do not exceed their weight limits, preventing overloading and the associated risks.
- Optimizing Load Positioning: Load sensing technology allows for the precise positioning of loads, reducing the potential for spillage or product damage.
Automation for Efficiency and Safety
Reducing Manual Handling Risks through Automation
Automation systems can take over repetitive and potentially hazardous tasks, reducing the need for manual handling. Benefits include:
- Safety: By automating tasks like material positioning and transport, the risk of operator injuries is minimized.
- Efficiency: Automation systems work with precision and consistency, optimizing productivity and reducing the margin for error.
Benefits of Load Positioning and Balancing Systems
Load positioning and balancing systems are designed to maintain the stability of loads during material handling:
- Stability: These systems ensure that loads remain stable and do not sway during transport, preventing product damage and enhancing safety.
- Reduced Downtime: Improved load stability means fewer incidents of product spillage or damage, reducing downtime for cleanup and maintenance.
Anti-Sway Technology and Load Monitoring
Enhancing Load Stability and Preventing Product Damage
Anti-sway technology is instrumental in maintaining load stability during crane operations. This technology can be particularly beneficial when handling sensitive products in flour mills:
- Product Integrity: Anti-sway systems prevent loads from swinging or swaying, safeguarding the integrity of the product.
- Preventing Product Damage: Swaying loads can lead to product spillage or damage. Anti-sway technology reduces these risks.
Real-Time Monitoring for Precise Operations
Real-time monitoring systems continuously track crane and load performance, providing critical data for precise operations:
- Safety: Monitoring systems alert operators to any potential issues or anomalies during crane operations, enabling swift corrective action.
- Efficiency: By providing real-time information, these systems assist operators in making precise movements and optimizing material handling processes.
Incorporating advanced technology into overhead crane operations is more than a modernization trend; it's a strategic move to enhance safety, precision, and efficiency in flour milling. By embracing remote control, load sensing, automation, anti-sway technology, and load monitoring, flour mills can stay at the forefront of technological advancements in the industry.
Compliance and Responsibility
Compliance with local regulations and a strong sense of environmental responsibility are integral to the sustainable and safe operation of flour mills. Additionally, analyzing past crane safety incidents through case studies offers valuable insights for ongoing improvement.
Adherence to Local Regulations
Safety and Environmental Standards in Flour Milling
Flour mills operate within a regulatory framework that governs both safety and environmental considerations. Adherence to these standards is vital and involves the following:
- Safety Regulations: Flour mills must comply with industry-specific safety regulations to ensure the well-being of their workforce and safe crane operations in potentially explosive environments.
- Environmental Regulations: Environmental responsibility is a fundamental aspect of flour milling, given the proximity of many mills to residential areas. Compliance with regulations governing emissions, waste management, and noise control is crucial.
Environmental Impact and Responsibility
Sustainability Initiatives in the Industry
Flour mills are increasingly embracing sustainability initiatives to minimize their environmental footprint and contribute to a healthier planet. Key points to consider include:
- Resource Efficiency: Reducing resource consumption, such as energy and water, helps mills operate more sustainably.
- Waste Reduction: Implementing strategies to minimize waste generation and improve waste management practices is a responsible approach to environmental impact.
Case Studies and Lessons Learned
Analyzing Past Crane Safety Incidents for Continuous Improvement
The study of past crane safety incidents is a critical aspect of responsible mill operation. By analyzing these incidents and learning from them, mills can continuously improve their safety protocols and crane operations. Considerations include:
- Root Cause Analysis: Understanding the root causes of past incidents provides valuable insights for preventive measures and safety enhancements.
- Process Enhancements: Lessons learned from past incidents can lead to process improvements, which, in turn, contribute to a safer and more efficient work environment.
- Preventive Measures: The knowledge gained from case studies can inform the implementation of preventive measures, reducing the likelihood of similar incidents in the future.
Compliance with regulations, environmental responsibility, and the analysis of past crane safety incidents are essential components of a flour mill's commitment to safety, sustainability, and continuous improvement. Flour mills that uphold these principles contribute not only to the well-being of their communities but also to the industry's long-term success and positive environmental impact.
Conclusion
As we draw this exploration of the relationship between flour mills and overhead cranes to a close, it becomes evident that these two elements share a flourishing partnership. The synergy of safety, efficiency, and innovation has paved the way for the continued success of the industry. Flour mill overhead cranes play a vital role in this partnership, navigating the unique challenges posed by the specialized nature of flour mill material handling.
Flour Mills and Overhead Cranes: A Flourishing Partnership
The Ongoing Role of Cranes in the Industry's Growth and Success
The partnership between flour mills and overhead cranes is enduring and essential. Cranes are the workhorses that facilitate the smooth flow of materials in an industry that is integral to global food production. Flour mills rely on cranes to ensure the efficient handling of raw materials, the precise positioning of machinery for maintenance, and the safe transportation of the final product.
The role of cranes in the industry's growth and success is multifaceted. Cranes contribute to:
- Increased Productivity: By streamlining material handling and maintenance, cranes boost productivity and reduce downtime.
- Product Quality: Precise material handling and minimal product damage ensure the quality and integrity of the flour.
- Safety: Safety is paramount in flour mills, and cranes play a critical role in minimizing accidents and protecting the workforce.
Prioritizing Safety, Efficiency, and Innovation
The Synergy of Safety and Productivity
Flour mills have learned that safety and efficiency are not opposing forces but allies. A safer work environment results in a more efficient and productive one. Flour mills that prioritize both safety and efficiency benefit from:
- Reduced Downtime: Safety measures prevent accidents and equipment damage, reducing costly downtime for repairs and maintenance.
- Employee Well-being: Prioritizing safety fosters a culture of well-being, reducing accidents and promoting employee satisfaction.
- Innovation: The industry continues to innovate, adopting advanced technologies and practices to improve safety, efficiency, and sustainability.
Flour Mill Overhead Cranes: Navigating Unique Challenges
The Specialized Nature of Flour Mill Material Handling
Flour mills operate in a specialized environment with unique challenges, the most prominent being the presence of potentially explosive flour dust. Overhead cranes designed for flour mills must navigate these challenges through:
- Explosion-Proof Features: Specialized cranes equipped with explosion-proof components and enclosures are essential for preventing dust-related accidents.
- Precision Load Control: Maintaining load stability and preventing overloading is crucial for product integrity and safety.
- Modernization with Technology: Flour mills are harnessing advanced technology and automation to enhance safety, efficiency, and precision in material handling.
In conclusion, the partnership between flour mills and overhead cranes is not just about lifting and moving materials; it's about ensuring the safety of the workforce, preserving product quality, and contributing to the industry's growth and success. Flour mills that navigate the unique challenges of their specialized environment with innovation and a commitment to safety will continue to flourish in an ever-evolving industry.