Overhead Cranes for Oil Refineries | Types & Selection Tips
Comprehensive Guide to Overhead Crane Operations in Oil Refineries
Oil refineries are intricate industrial hubs where the transformation of crude oil into various valuable products occurs. Amidst this complex process, one unsung hero stands tall—overhead cranes. These engineering marvels play a pivotal role in handling heavy equipment, aiding in construction, facilitating maintenance tasks, and ensuring efficient material handling throughout the refinery.
Crucial to the success of refinery operations is the selection of the right type of overhead crane, tailored to meet specific operational demands. Choosing the appropriate crane type can significantly impact productivity, safety, and overall efficiency within the refinery setting.
The Significance of Overhead Cranes in Oil Refinery Operations
Imagine the labyrinthine expanse of an oil refinery, where towering structures and intricate machinery form the backdrop of a dynamic production environment. Within this landscape, overhead cranes emerge as indispensable workhorses, serving multifaceted purposes that are pivotal at different stages of the refining process.
These cranes encompass a diverse range of types, each designed to tackle distinct tasks within the refinery. From the lifting of heavy equipment during construction to the precise handling of materials in workshops, these cranes are the silent backbone of refinery operations.
At the heart of efficient refinery operations lies the careful selection and utilization of overhead cranes. Each crane type boasts unique functionalities and capabilities, making it imperative for refinery managers and operators to comprehend their diverse applications and select the appropriate crane for each operational phase.
Importance of Choosing the Right Crane Type
Selecting the right crane type is akin to choosing the right tool for a specific job. Refinery operations vary significantly, from construction and installation phases to ongoing maintenance activities and material handling within different workshops or storage areas. The choice of crane directly impacts efficiency, safety, and the ability to meet operational demands effectively.
An inadequate crane type may lead to bottlenecks, operational delays, compromised safety, and potential damage to equipment or materials. Therefore, understanding the distinct features and functionalities of each crane type is crucial for ensuring seamless refinery operations.
Types of Overhead Crane Operations in Oil Refineries
Overhead cranes are the backbone of efficient material handling within oil refineries. They come in various types, each meticulously designed to serve specific purposes in refinery operations. Understanding the distinctions between these crane types is paramount to optimizing their use in different refinery scenarios. Let's explore the diverse array of overhead cranes used in oil refineries:
- Overview: Top Running Cranes are characterized by their ability to run along the top of the runway beams. They are renowned for their robustness and are ideal for handling heavy loads.
- Functions and Applications: Top Running Cranes excel in heavy lifting operations, transporting large equipment, and handling substantial loads during construction and maintenance within the refinery.
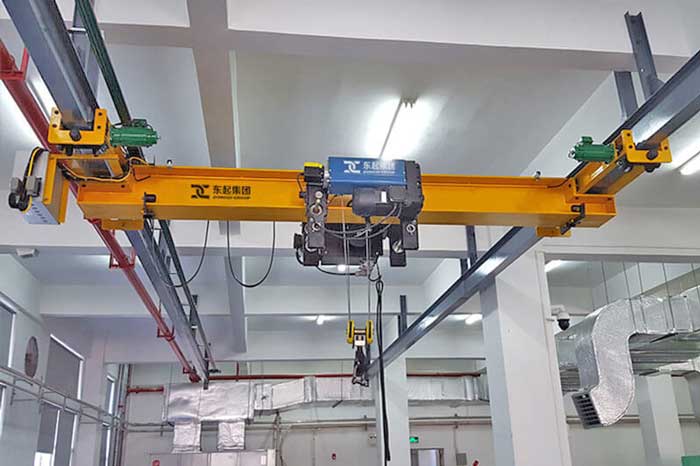
- Overview: Underhung Cranes have their wheels or end trucks attached to the bottom flange of runway beams. They are suitable for areas with limited headroom or where integration into existing structures is essential.
- Functions and Applications: These cranes are utilized in workshops, smaller storage areas, or locations with limited space within the refinery, offering moderate load handling capabilities.
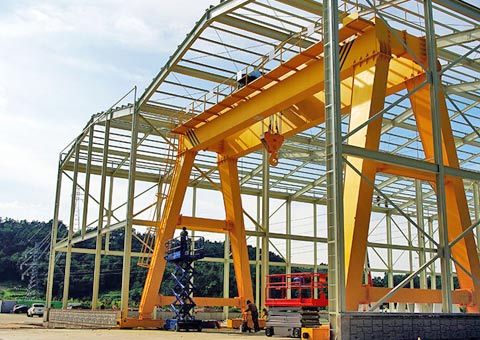
- Overview: Gantry Cranes feature a bridge that spans between two supporting legs. They find extensive use in tank farms for loading, unloading, and handling heavy loads.
- Functions and Applications: Gantry Cranes are indispensable for handling bulk materials, containers, or drums within the tank farm operations of the refinery.
- Overview: Jib Cranes have a vertical mast or wall-mounted structure with a rotating boom, allowing precise lifting and placement of equipment or materials in specific refinery locations.
- Functions and Applications: These cranes are crucial for localized material handling, offering precise positioning during assembly, maintenance, or repair operations within the refinery.
- Overview: Explosion-Proof Cranes are designed to operate safely in environments where the presence of flammable gases, vapors, or dust could lead to an explosion.
- Functions and Applications: They find applications in areas where flammable substances are present, such as processing units or chemical storage areas in refineries.
- Overview: Grab Cranes are specialized with a grab or grapple attachment at the end of the lifting mechanism, allowing them to grasp and lift bulk materials.
- Functions and Applications: Used for loading/unloading bulk materials like coal, ore, or other granular materials in refinery storage yards or processing units.
Functions and Applications of Overhead Cranes in Oil Refineries
Overhead cranes in oil refineries serve as indispensable tools across various operations, providing crucial support at every stage of the refining process. Each type of crane exhibits unique capabilities tailored for specific tasks within the refinery setting. Let's explore the diverse applications and functions of overhead cranes in different refinery operations:
Construction and Installation Phase
- Top Running Cranes: Used for lifting heavy equipment, transporting construction materials, and placing structural components during refinery erection.
- Gantry Cranes: Aid in the construction of storage tanks, handling heavy materials, and assisting in the assembly of refinery structures.
Maintenance and Repair Activities
- Underhung Cranes: Ideal for maneuvering in tight spaces during maintenance tasks, lifting tools, and supporting equipment repair operations.
- Jib Cranes: Precisely handle replacement parts, assist in maintenance procedures, and provide localized lifting support for repair activities.
Material Handling in Workshops
- Top Running Cranes: Efficiently move materials, tools, and components in workshops, ensuring smooth workflow and enhancing productivity.
- Grab Cranes: Used in workshop areas for handling raw materials or finished products during manufacturing processes.
Tank Farm Operations
- Gantry Cranes: Essential for loading/unloading bulk materials, containers, or drums in tank farms, optimizing storage and distribution processes.
Loading/Unloading of Raw Materials
- Grab Cranes: Handle loading/unloading of bulk materials such as coal, ore, or granular substances in refinery storage yards or processing units.
Handling Finished Products
- Underhung Cranes: Assist in the handling and packaging of finished products, ensuring precise placement and organized storage.
Each type of overhead crane offers distinct functionalities that cater to specific tasks within oil refineries. Understanding their applications aids in maximizing efficiency and safety across different refinery operations.
Choosing the Right Crane for Specific Refinery Needs
In selecting the appropriate crane system for oil refineries, several critical factors must be meticulously considered to ensure optimal performance, safety, and operational efficiency.
Factors to Consider for Buyers
- Refinery Size and Scale: Assessing the dimensions and layout of the refinery is imperative. Larger refineries may require heavy-duty cranes capable of handling substantial loads and extended reach, while smaller facilities might benefit from more compact, versatile crane systems.
- Location and Environmental Conditions: Refineries situated in diverse environments, such as coastal areas or regions prone to chemical exposure, demand specialized cranes equipped to withstand corrosive elements or explosion risks. Considering these environmental factors is crucial in selecting the appropriate crane with suitable coatings or construction materials.
- Types of Materials Handled: Understanding the diversity of materials handled within the refinery - be it raw materials or finished products - is pivotal. Different cranes are designed to handle specific materials efficiently. For instance, handling large vessels requires cranes with higher load capacities, whereas precision handling of sensitive components necessitates precise controls.
- Required Lifting Capacity and Reach: Determining the lifting capacity and reach needed for various operations within the refinery is essential. Different crane types offer varied load capacities and reach capabilities. Selecting the crane system that aligns with these specific requirements ensures seamless and efficient material handling.
- Safety and Compliance with Industry Standards: Compliance with stringent safety standards is non-negotiable within refinery settings. Choosing crane systems that adhere to industry safety regulations and standards mitigates risks and ensures a safer working environment.
Guidance on Crane Selection
- Refinery Construction and Installation Phases: For heavy lifting during construction, top-running cranes with substantial load capacities and extensive reach are advisable.
- Maintenance and Repair Activities: Jib cranes, known for precise handling in confined spaces, are ideal for maintenance areas where precision is crucial.
- Tank Farm Operations: Gantry cranes, with their ability to load and unload bulk materials, are well-suited for tank farm operations requiring extensive reach and load capacities.
- Handling Hazardous Materials: Explosion-proof cranes, engineered with safety features, are recommended for areas at risk of explosions, ensuring secure material handling.
- Corrosive Environments: Corrosion-resistant cranes, tailored for durability in corrosive atmospheres, are indispensable in coastal refineries or areas prone to chemical exposure.
By aligning the selection of crane types with specific refinery needs and operational demands, oil refineries can optimize material handling efficiency while ensuring safety and compliance with industry standards.
Crane Installation and Maintenance
The installation and maintenance of overhead cranes in oil refineries are critical steps that ensure their efficient and safe operation throughout their lifespan. Understanding proper installation and maintenance procedures is vital for refinery operators and maintenance personnel.
Installation Guidelines
Proper Setup and Installation Procedures:
- Each crane type has specific installation requirements; following manufacturer guidelines is crucial.
- Ensuring structural integrity, appropriate positioning, and correct assembly of components for safe crane operation.
Safety Measures during Installation:
- Adhering to safety protocols, including the use of appropriate personal protective equipment (PPE) during installation.
- Conducting installation under the supervision of qualified personnel to prevent accidents or structural issues.
Maintenance Procedures
Regular Maintenance Schedules and Checks:
- Implementing routine inspection schedules to identify wear and tear, loose components, or potential issues.
- Lubrication, checking electrical systems, and inspecting load-bearing parts for signs of damage.
Ensuring Compliance with Safety Regulations:
- Following safety regulations and manufacturer recommendations for maintenance practices.
- Conducting maintenance checks in line with industry standards and specific crane type guidelines.
Importance of Proper Installation and Maintenance
- Prolonged Lifespan: Correct installation and regular maintenance significantly extend the crane's lifespan, reducing downtime and replacement costs.
- Safety Assurance: Properly installed and maintained cranes ensure safe operations, mitigating the risk of accidents or malfunctions.
- Optimized Performance: Regular maintenance enhances crane performance, ensuring reliability and efficiency in refinery operations.
Refinery personnel responsible for crane operations and maintenance should prioritize proper installation and adherence to maintenance schedules. It's crucial to invest time and resources into these procedures to guarantee the longevity, safety, and efficient functioning of overhead cranes within oil refineries.
Safety Protocols and Training for Crane Operators
Safety protocols and operator training are fundamental aspects of overhead crane operations in oil refineries. Ensuring that crane operators are well-trained and equipped with comprehensive safety knowledge is paramount to prevent accidents and maintain a secure working environment.
Importance of Operator Training
Proper Training Programs for Crane Operators:
- Structured training programs focusing on crane operation, load handling, and understanding crane functionalities.
- Emphasis on safety guidelines, emergency procedures, and protocols specific to different crane types.
Safety Protocols and Best Practices during Crane Operations:
- Educating operators on safety protocols, including load weight limitations, avoiding sudden movements, and conducting pre-operation checks.
- Emphasizing the importance of clear communication between operators and ground personnel during crane operations.
Preventative Measures for Safe Operations
Adherence to Safety Regulations:
- Ensuring compliance with safety regulations, industry standards, and refinery-specific safety protocols.
- Regular safety audits to identify potential hazards and address safety concerns promptly.
Continuous Training and Skill Development:
- Encouraging ongoing education and skill enhancement for crane operators to keep abreast of new safety measures and technological advancements.
Use of Safety Equipment and Tools:
- Mandating the use of appropriate safety equipment, such as harnesses, hard hats, and safety goggles, to protect operators and personnel.
Ensuring Safe Handling of Loads
Proper Load Inspection and Handling:
- Training operators in load inspection procedures to identify potential hazards before lifting.
- Emphasizing the importance of even load distribution and secure rigging during lifting operations.
Emergency Preparedness and Response:
- Conducting drills and training exercises to prepare operators for emergency situations and ensuring swift, effective responses to mitigate risks.
Incorporating robust operator training programs and stringent safety protocols is crucial for maintaining a safe working environment and preventing accidents during overhead crane operations within oil refineries.
Conclusion: Get Your Overhead Crane Design for Specific Oil Refineries
The comprehensive guide to overhead crane operations in oil refineries has provided a comprehensive overview of the diverse crane types, their functions, specific applications across various refinery operations, safety protocols, and real-life examples. Let's summarize the key takeaways:
- Diverse Crane Types and Functions: - Overhead cranes such as Top Running, Underhung, Gantry, Jib, Explosion-Proof, Corrosion-Resistant, and Grab Cranes cater to specific tasks and operational needs within oil refineries.
- Applications Across Refinery Operations: - Cranes play pivotal roles in construction, maintenance, material handling, tank farm operations, loading/unloading raw materials, and handling finished products within refineries.
- Choosing the Right Crane: - Factors like refinery size, environmental conditions, material handling requirements, lifting capacity, and safety compliance guide the selection of the most suitable crane type for specific refinery needs.
- Installation and Maintenance Importance: - Proper installation and regular maintenance procedures are critical for ensuring crane efficiency, safety, and prolonged lifespan within refinery environments.
- Safety Protocols and Operator Training: - Operator training, adherence to safety protocols, and continuous skill development are imperative to prevent accidents and ensure safe crane operations.
As technology evolves and refining processes advance, the role of overhead cranes in oil refineries continues to evolve. It is crucial to remain adaptable, continuously learn, and embrace innovations to meet the ever-changing demands of the refining industry.